I believe everyone has read a lot of related introductions about the working principle of laser marking machines. At present, it is generally recognized that the two types are thermal processing and cold processing. Let’s look at them separately:
The first type of "thermal processing": it has a laser beam with a higher energy density (it is a concentrated energy flow), irradiated on the surface of the material to be processed, the surface of the material absorbs the laser energy, and generates a thermal excitation process in the irradiated area, thereby Raise the temperature of the material surface (or coating), resulting in metamorphosis, melting, ablation, evaporation, and other phenomena.
The second type of "cold processing": it has very high energy load (ultraviolet) photons, which can break the chemical bonds in materials (especially organic materials) or surrounding media, to cause non-thermal process damage to materials. This kind of cold processing has special significance in laser marking processing, because it is not thermal ablation, but a cold peeling that does not produce "thermal damage" side effects and breaks chemical bonds, so it is not harmful to the inner layer and nearby areas of the processed surface. Produce heating or thermal deformation and other effects.
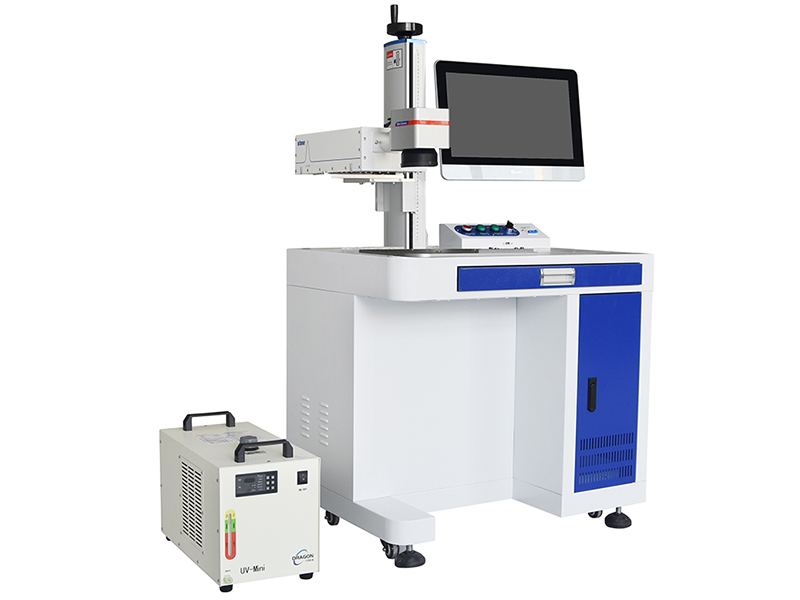
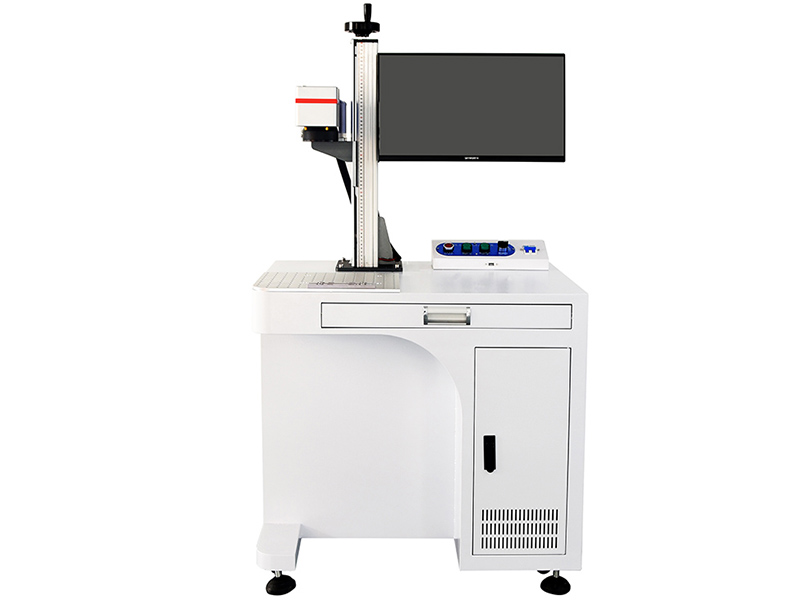
Post time: Feb-27-2023